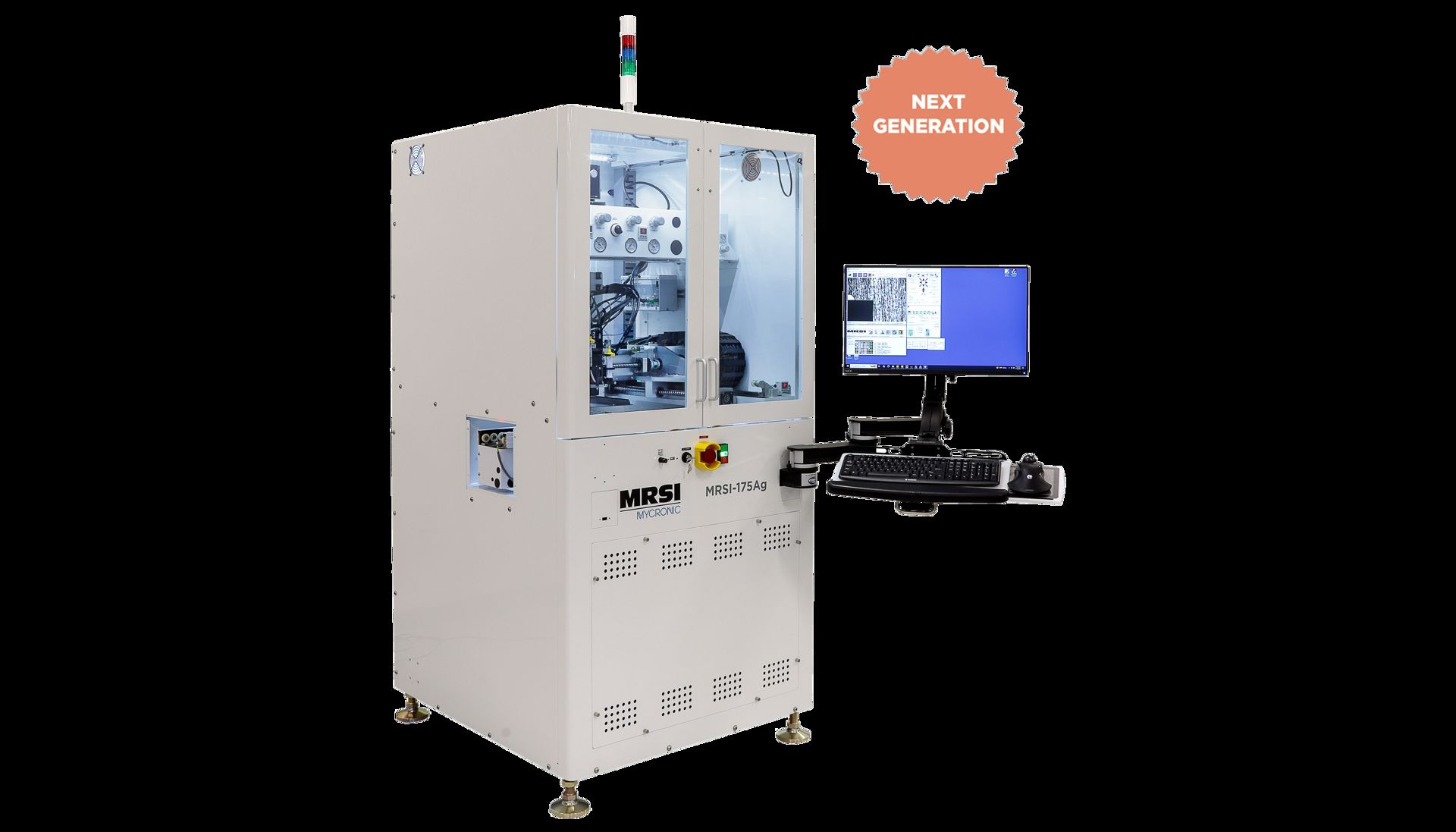
Next Generation Epoxy Dispenser MRSI-175Ag
- Up to 10x faster than previous generation
- 10µm accuracy option available
- 35% more energy efficient
The next generation MRSI-175Ag Epoxy Dispenser handles the most demanding dispensing applications such as advanced packaging, microwave modules, optical modules, hybrid circuits, multichip modules, and semiconductor packaging. With the ability to operate two heads in tandem, the MRSI-175Ag provides unparalleled process control and comprehensive dispensing capability. Die attach, underfill, encapsulation, and multi-pin stamping are all supported on this flexible dispensing platform.
The MRSI-175Ag Epoxy Dispenser is a high-performance model offered by MRSI Systems. It is a pneumatic dual epoxy dispenser. This type of dispensing system is known for its speed and precision, making it a popular choice in industrial settings. This model is specifically designed for dispensing silver-filled epoxies, making it ideal for use in electronics and other applications where a high-conductivity epoxy is required. In addition to its pneumatic dual head design, it also features a controlled volume dispensing system proven to be highly repeatable, fast and accurate.
The MRSI-175Ag is a servo-controlled X, Y, and Z dispensing platform. The machines' two dispensing heads can be individually configured with various pump types, such as positive displacement, time/pressure, and jetting. A stamp head is also available with the capability to repeatedly stamp dots as small as 0.1mm. Dots of silver-filled conductive epoxy of 0.2mm diameter are quickly and routinely dispensed by the system; a requirement frequently encountered for the assembly of microwave modules, as well as other advanced packages. Precise epoxy flow control is necessary to meet tight bond line thickness specifications while achieving 100% area coverage.
Driven by MRSI Systems’ Windows software, the MRSI-175Ag delivers a clean, easy-to-use interface, providing easy access to extensive process control functions, as well as product programming capabilities. The software is common to all MRSI Systems’ machines.
MRSI-175Ag+ is an available option with 10µm accuracy.
Benefits
As with all other MRSI platform offerings, the next generation MRSI-175Ag is built to last. Flexibility is built-in, with the ability to dispense two different materials, with different dispensing parameters, on any given application. Attention is given to automation, reducing operator intervention and machine downtime. Adding an MRSI-175Ag epoxy dispenser to your existing manufacturing line upstream from an MRSI-M3 3-Micron Die Bonder or an MRSI-705, increases line efficiency and throughputs with a minimum investment.
Advanced functionality equates to significant operational and financial benefits:
- Increase capacity at lower cost – Separating the dispensing process step from the placement operation translates into lower costs by leveraging both machine types for what they do best.
- Less Labor Cost – Automatic needle cleaning, automatic calibration routines mean less operator intervention and higher productivity.
- Lower Cost of Ownership – Commonality with MRSI placement machines means lower spare parts cost, lower parts inventory, lower training costs.
- Higher Yields – High precision, automated process control functions, proven pump technology all come together to ensure maximum yields, which in turn translates into a lower cost per part.
- Flexibility – Handle whatever comes your way with the ability to use the right pump for the right application. Reconfigure if needed.
- More Energy Efficient – 35% more energy efficient compared to previous generations.
- Ergonomic – Easier to operate and access key areas.
- Ultra-high speed – Up to 10x faster than previous generation.
- Accuracy – 25µm standard, 10µm option available.
The base MRSI-175Ag comes already equipped with industry-leading functionality. Additional capability is available to reflect specific application needs.
Features
The base next generation MRSI-175Ag comes already equipped with industry-leading functionality. Additional capability is available to reflect specific application needs. Standard Features include:
Large Work Area
The MRSI-175Ag handles large boards, fixtures, or boats.
The system operates as a stand-alone dispensing station, or when in inline conveyor mode, as an upstream or downstream epoxy dispenser linked with other manufacturing equipment.

Vision Alignment
Tri-color (red, green, and blue) stadium lighting is combined with a collimated light source that incorporates programmable lighting intensity to enable the processing of the widest range of die, substrates and packages.
Global and local vision alignments are used for nested substrates and features. This enables and fast error free processing of complex assemblies.

Height Sensing
The MRSI-175Ag is the only dispenser with a substrate surface mapping ability through laser height sensing. The system uses a laser to sense height in three locations, thereby determining the tilt of the surface on which material will be dispensed. An unlimited number of surfaces are mapped within a package. Surface mapping enables precise gap control during dispensing. This is especially valuable when dispensing on substrates that were manually mounted in a previous process.
In cases where laser triangulation is limited, MRSI systems offer the option of using a Confocal Height Sensor to establish the dispense height in a single axis. The unique approach provides the capability to dispense adhesives into deep cavities and channels, such as those commonly found in RF microwave packages.

Process Control
The MRSI-175Ag features high-resolution servo driven, positive displacement pumps, for the most accurate dispensing of dots, lines and areas.
A time/pressure or jet pump can also be integrated into the system, depending on the application, materials and process requirements.

Calibration
Automatic needle calibration enables fast changeover between applications.
Cleaning
Automatic needle cleaning eliminates material build-up on the tip. Needle cleaning steps are automatically turned on during the dispense program to enable smooth transitions between area fills and small dots.

Priming
Automatic needle priming assures precise dispensing.

Dispense Needles
Choose from a broad range of application specific needles including tapered needles, polished needles and “footed” needles.
MRSI Systems Windows Software
The MRSI-175Ag’s intuitive graphical user interface, running on Windows™ simplifies the set-up and production process. The software includes a pre-programmed library of dots, lines, area fills, spirals, arcs, and star patterns.
An easy to use tool makes these patterns easily customized to fit the application. Once taught, dispense programs are quickly optimized. Calibration routines, offline programming, and CAD download mean little time is spent programming and more time is available for production. Dispense programs generated on the MRSI-175Ag can be used to create placement programs on the MRSI Die Bonders.
Turnkey Integrated Production Lines
The MRSI-175Ag is the perfect companion to other MRSI Systems assembly equipment since it shares the same software platform and is SMEMA compatible. It can also be combined with other manufacturers’ SMEMA compatible units for a complete production line.
Options
MRSI's systems may be configured with off-the-shelf options to meet application-specific needs, a cost effective alternative to custom automation. The base platform comes equipped with standard features . The machine can then be configured in various ways with one or a combination of the following options:
Material Handling
Tooling is modular, ensuring fast, easy change-over between production runs – In addition to standalone mode, the MRSI-175Ag epoxy dispenser supports two modes of operation when it comes to product presentation. They are cassette-to-cassette and inline conveyor modes.
Cassette to Cassette: The product to be processed is stacked in cassettes. The cassette(s) contains multiple boats or common carriers, which hold the individual substrate(s). The input loader indexes the cassette(s) up and down and pushes the boat or common carrier from the cassette onto the material handling conveyor. Customers can supply their own cassettes or magazines or it can form part of this options package. The material handling conveyor transfers the boat or common carrier holding the substrates to the work area. The assembly station (i.e. fixturing, personality plate) lifts to hold the parts for processing (e.g. dispensing, assembly, etc.). After the process is completed, the conveyor transfers the boat or common carrier to the output cassette. Customers can supply their own boats or these can be designed by MRSI.
Inline – Setup the MRSI-175Ag epoxy dispenser to operate upstream or downstream from other machines, such as one of the MRSI placement systems. The adjustable width, in-line conveyor transports boats, common carriers, or lead frames. Tooling is modular for easy change-over between production runs.
Benefits:
- Easily integrated into automated production lines, both the in-line and cassette-to-cassette tooling options allow for greater machine autonomy, translating into a workload reduction and less setup downtime.
- Existing customer tooling, used upstream and or downstream from the dispenser, can be adapted; allowing streamlined product handling strategies to be implemented. Less product transfer means less operations, lower handling defect rates and improved cycle time

Second Head Epoxy Stamping Package
With this option, hardware for epoxy stamping is mounted in substitution of the second dispense head. Stamping of epoxy dots as small as 0.004” (100 microns) is achieved. Sequentially, the stamping tool is dipped into a rotating well to pick up epoxy (1) based on surface tension; the head then moves to location (2) and the material is then released to the substrate, again through surface tension (3).
Two different epoxy materials may be transferred simultaneously, using separate well reservoirs.
Different dot dimensions are obtained by adjusting the height of a wiper blade, which controls the amount of material in the epoxy well, and therefore the amount of material transferred onto the stamping tool. The stamping package option includes the stamping head itself, stamping tools and the epoxy well(s). Custom stamping tools are also an available option.
Benefits:
- Choose the process that fits the application. Stamping for small dots or Dispensing. You will be ready for anything that comes your way!
- Control the costs by controlling the process. High yields mean reduced costs.
- Get better use of your existing productions lines by adding a dispensing tool with stamping options. Increase the line throughput by doing so.

Heated Rotary Pump
Dispense pumps and needles are heated via a closed loop thermal controller. Independent temperature settings can be set for the pump body and the needle.
Benefits:
- Ability to dispense materials at temperature. Choose optimum temperature for a given material.
- Better process control by separate settings for pump and needle.
Dual Real Time Video
The MRSI-175Ag epoxy dispenser is available with dual real time video. The system automatically switches between dispense tips to focus on the tip currently being used. This tool enables constant process monitoring.
Benefits:
- Real Time Process Monitoring. You can always verify that the process is under control.
- Less rework due to incomplete processing.

Confocal Height Sensor
A confocal chromatic sensor is used to precisely determine dispense heights. The confocal sensor allows measurements in a single axis providing access to deep cavities and in close proximity to walls and other obstructions. The sensor can accurately map areas not accessible to a laser triangulation system.
An LED light source with a sensor spot size of 50 microns in diameter is utilized to provide nanoresolution that is target independent. The confocal sensor allows accurate measurement of glass, semiconductor materials and mirrored surfaces.
The sensor has a measurement range of 10 mm with a resolution of 0.4 microns at 0.004% Full Scale Output. All data is at a constant ambient temperature against an optical flat at 2kzHz, and specifications can change when measuring different materials.
Benefits:
- Handle applications that are normally out-of-reach
- Better yields through advanced sensor technology.

Time/Pressure Dispense
Hardware for a time/pressure dispense head is provided with the system. This includes the flexibility to add a second time/pressure dispense head for dispensing two epoxies (e.g., conductive and non-conductive). The option includes the mounting hardware for Time Pressure Dispensing head(s).
Benefits:
- Adaptable to a range of dispensing approaches.
- Lower costs of dispensing equipment and lower maintenance costs.

Jet Dispense Package
Hardware for a jet pump dispense pump is mounted on the head. This option includes the mounting hardware and a second head with a jet pump with encoder feedback.
Benefits:
- Adaptable to a range of dispensing approaches.
- Achieve high throughputs typically associated with jetting.

Videos
Brochures
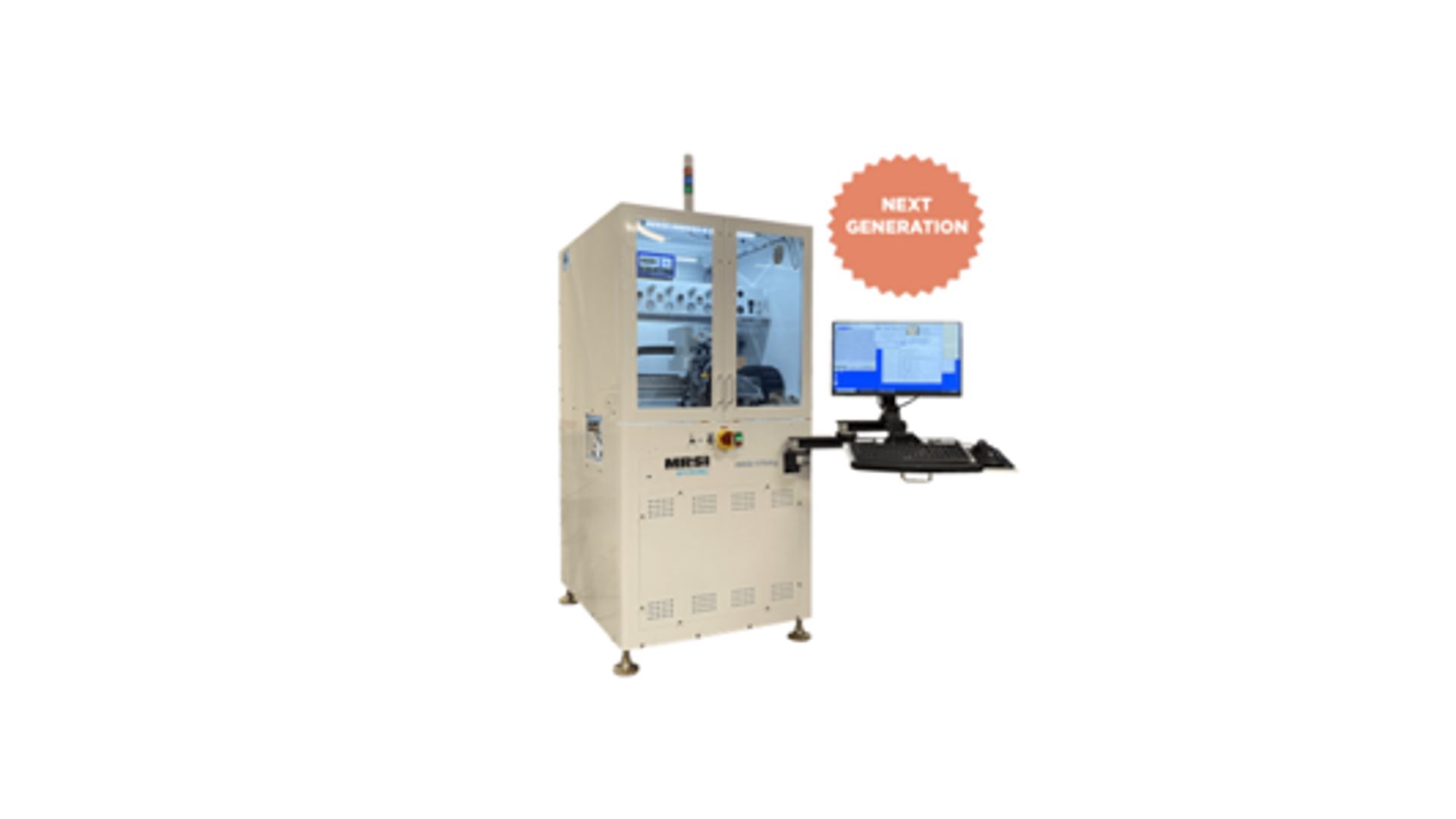
Next Generation MRSI-175Ag
For detailed Data Sheets please contact Sales.
Next Generation MRSI-175Ag
Contact us
