The new MX7 mounthead
Mount a far wider range of components at 48% higher top speeds. The MX7 mounthead technology is the fast-beating heart of the next-generation MYPro A40 pick-and-place machines, making it possible to simultaneously boost production volumes and take on more jobs. Driven by seven high-precision nozzles and fourteen independent motors, the MX7 represents a leap forward in performance and versatility.
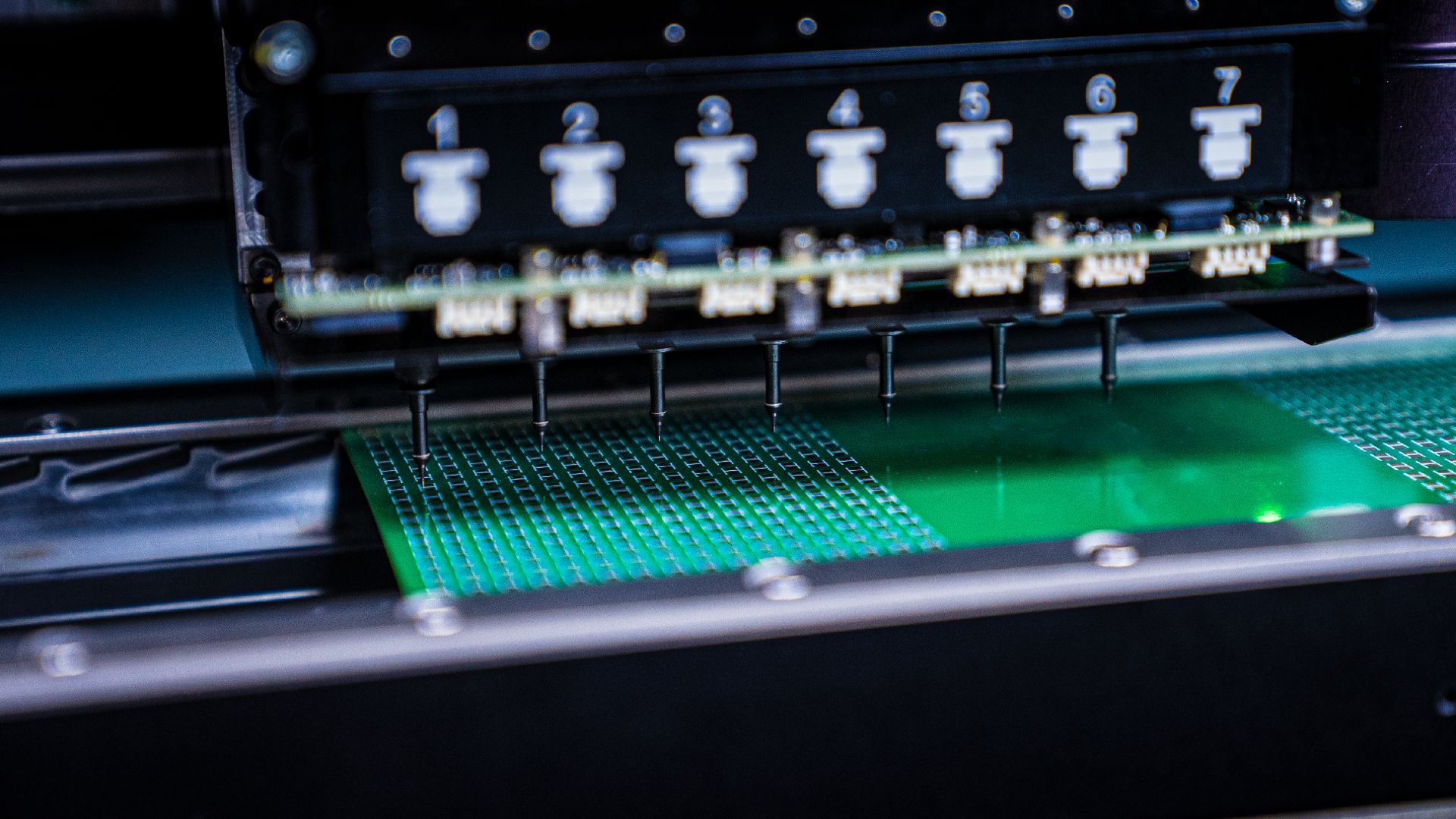
A new generation of flexible, high-speed pick-and-place technologies is here. The result of several years of in-house development, the new MX7 mounthead technology goes further than ever before in bridging the gap between high-mix and high-volume PCB assembly.
Parallel precision
At the core of the MX7 are fourteen independently controlled Z and theta motors, making it one of the world's first multi-axis pick-and-place technologies. Each of these motors is individually guided, enabling much more reliable and repeatable placement in both the Z and theta axes. This level of granular control is unprecedented in the industry and opens up new possibilities for high-precision assembly.
Mount virtually any component
The MX7 mounthead takes flexibility to the next level, enabling the handling of component sizes up to 45×45×15 mm or 150×40×15 mm, and down to 01005 (0.4×0.2 mm). This amounts to a substantial increase in the range of component types and sizes mounted by a single platform, making the MYPro A40 a versatile solution for a wide range of applications. Whether you're dealing with fine-pitch CSPs, FCs, BGAs, or larger, odd-shaped components, the MX7 can handle them all while minimizing the risk of damaging, mis-picking or dropping parts.
80,000 updates per second
Increased speed was one of the key design objectives in the development of the new platform, resulting in a 48% increase in top placement speeds compared to previous high-speed mountheads. This boost in performance is made possible by an entirely new servo platform, which updates at a rate of 80,000 times per second in order to optimize every movement. In combination with state-of-the-art vision and pressure sensor systems, it allows for rapid pick-and-place operations without compromising accuracy or reliability.
Highlights of the new mounthead technology include
Higher throughput
The MX7 enables top placement speeds of 59,000 cph – a full 48% speed increase compared to its predecessor. In beta tests, the productivity increases are significantly higher, thanks to the platform’s ability to handle a wider range of components with less downtime in actual production conditions.
Gentler placement
To prevent component damage, each of the seven placement nozzles operates with a less than 2-newton placement force. At the same time, they eject a highly controlled stream of air during component placement, virtually eliminating the risk of unnecessary nozzle impact.
Advanced acceleration control
Despite its gentle touch, the MX7 mounthead unit is capable of up to 3G acceleration forces, making quick work of even the most complex board layouts.
Robust, low-maintenance construction
A combination of finely controlled vision and motion systems, together with a robust gantry platform, contributes to significantly lower maintenance and calibration requirements.
Six times larger components
Although the individual MX7 nozzles are spaced just 20 mm apart, the system is capable of mounting components up to six times larger than those placed by previous high-speed mountheads.
Innovative tools
A new range of unique tool types on the MX7 mounthead, together with new toolbanks for tool changes, ensures more precise component handling for a wider array of applications. Each nozzle is also equipped with a unique ID to improve process traceability and analysis.
* All MYPro A40DX models include two MX7 high-speed mountheads and one MIDAS high-precision mounthead.
Engineering a new generation of high-speed assembly
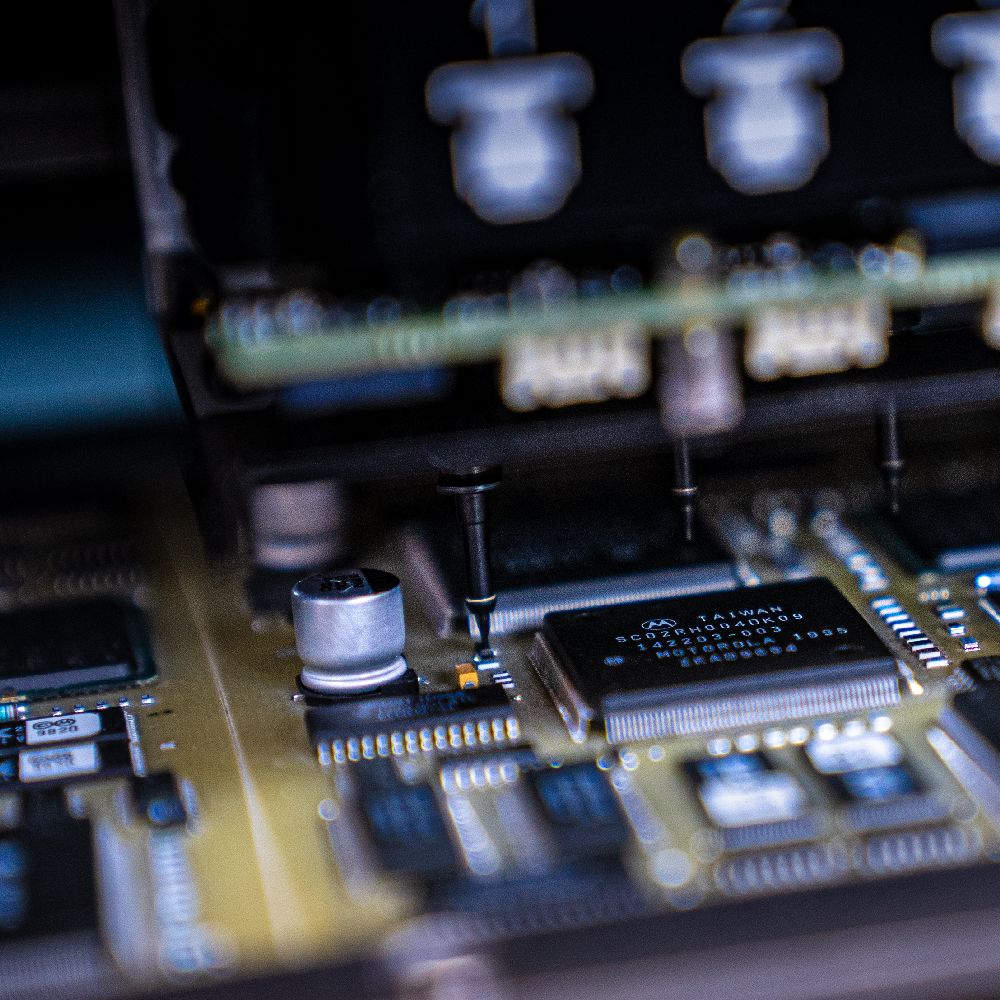
To solve these challenges, a number of innovative engineering solutions had to be developed from scratch, explains Tanaka. “First, we had to be very disciplined in reducing the weight of all the moving parts. Then, it was even more challenging to both miniaturize and find the ideal placement for the touch detection mechanism to ensure enhanced usability: one of the real trademarks of every Mycronic solution.”
“Fortunately, every engineer on our team has more than a decade’s experience solving exactly these challenges,” he concludes. “Everyone knew how long it takes to optimize a new head and system, so we factored in all the variables prudently and executed each plan carefully. And now, it’s paying off for Mycronic customers. I’m convinced the MYPro A40 and MX7 will impress the industry, taking PCB assembly to completely new heights.”